As early as the 1900’s, aluminum has been used in the construction industry. However it was not until the 1920’s, when the electrolysis process reduced the cost to produce aluminum by 80%, that aluminum became widely used in building construction. One of the most recognizable buildings in the world, the Empire State Building which was constructed in 1931, utilized aluminum in all of its basic structures and even on the famous Spire. Aluminum can also be found throughout the famous New York Skyscraper’s interior, most notably, on the lobby’s ceiling and walls. In 1993, the Empire State Building underwent a giant makeover resulting in even more aluminum: all 6,514 of the building’s windows had their iron frames replaced more efficient and lighter weight aluminum frames. Fast forward to modern day, and nearly a quarter of all aluminum produced in the world is used in the construction industry.
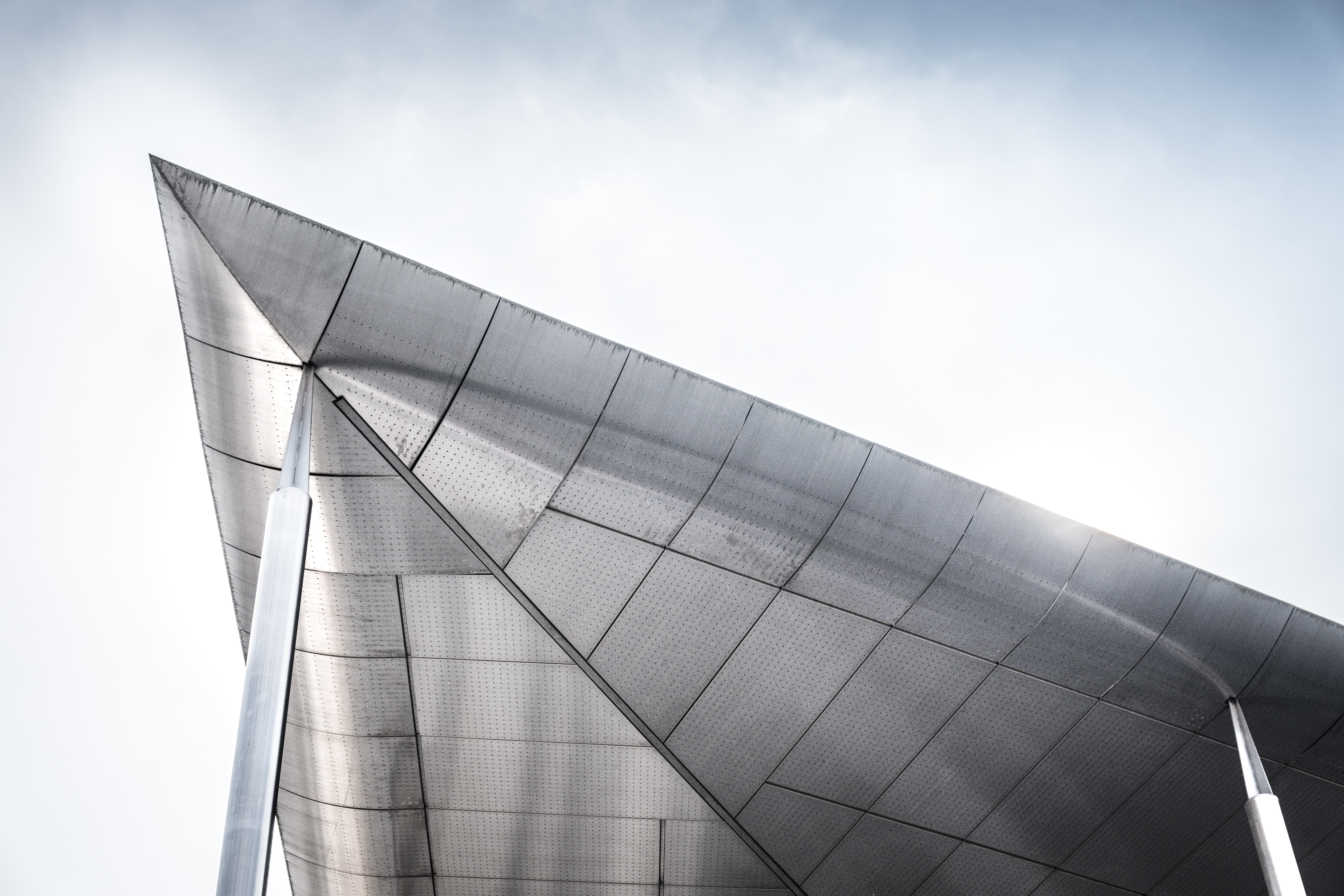
What Makes Aluminum So Valuable in Construction?
A light-weight and strong metal with natural corrosion resistance, aluminum is the third most abundant element on Earth. With additional properties such as high strength-to-weight ratio, durability, machinability, and reflectivity, aluminum alloys have become a building material of choice for applications such as siding material, roofing material, gutters and downspouts, window trim, architectural details, and even structural support for grid shell style architecture, drawbridges, high-rise buildings and skyscrapers. With aluminum, such as aluminum alloy 6061, it is possible to create structures that cannot be produced using other building materials such as wood, plastic or steel. Finally, aluminum is soundproof and airtight. Because of this feature, aluminum extrusions are commonly used as window and door frames. The aluminum frames allow for an exceptionally tight seal. Dust, air, water, and sound are unable to penetrate doors and windows when they are closed. Therefore, aluminum has cemented itself as a highly valuable building material in the modern construction industry.
6061: Strength and Corrosion Resistance
The 6000 aluminum alloy series is often used in large construction applications, such as those involving the structure of buildings. An aluminum alloy that utilizes magnesium and silicon as its primary alloying elements, aluminum alloy 6061 is highly versatile, strong, and lightweight. The addition to chromium to aluminum alloy 6061 results in high corrosion resistance which makes it an ideal candidate for building applications such as siding and roofing. With a high strength to weight ratio, aluminum offers almost the same strength as steel at only about half of the weight. Because of this, aluminum alloys are commonly used in high-rise structures and skyscrapers. Working with aluminum allows for a lighter weight, less expensive building, without a reduction to rigidity. All of this means that overall maintenance costs of aluminum buildings is minimal and the lifespan of the structures is longer.
Strength-to-Weight Ratio
Aluminum is exceptionally strong and very versatile. Weighing about the third of steel, aluminum is a top choice when weight needs to be shaved without and expense of strength. Not only is the lightweight and versatility helpful in building, but the lighter weight is also beneficial in the loading and transport of the material. Therefore, transport costs of this metal are less than other metal building materials. Aluminum structures are also easily dismantled or moved, when compared to steel counterparts.
Aluminum: A Green Metal
Aluminum has many characteristics that make it a green alternative. First, aluminum is non-toxic in any amount. Second, aluminum is 100% recyclable and can be recycled infinitely into itself without losing any of its properties. Recycling aluminum takes only about 5% of the energy necessary to produce the same amount of aluminum. Next, aluminum is much more heat reflective that other metals. This comes in handy when used in construction applications such as siding and roofing. While aluminum reflects heat, other metals, like galvanized steel, will absorb more of the heat and energy from the sun. The galvanized steel also rapidly loses more of its reflectivity as it weathers. In conjunction to heat reflectivity, aluminum is also less emissive than other metals. Emissivity, or the measure of the ability of an object to emit infrared energy, means heat radiating power and indicates the temperature of the object. For example, if you heat up two blocks of metal, one steel and one aluminum, the aluminum block will stay hotter longer because it radiates less heat. It is when the emissivity and reflecting properties are combined that aluminum is useful. For example, an aluminum roof will reflect the light from the sun and never get hot in the first place, which can decrease inside temperatures as much as 15 degrees Fahrenheit when compared to steel. Aluminum’s abundance, ability to be recycled, and properties make it the greener choice in building materials. Furthermore, it is because of these green properties that use of aluminum materials in building projects helps them qualify under LEED standards. LEED, Leadership in Energy and Environmental Design, was established by the U.S. Green Building Council in 1994 to encourage sustainable practices and design. Aluminum is a top building material of choice on LEED projects.
As a 100% aluminum distributor, Howard Precision Metals is the trusted source for aluminum plate, aluminum sheet and extruded aluminum shapes requirements. Next time you have an aluminum construction requirement, trust the experts at Howard Precision Metals.
Call us today at 800.444.0311 or request for quote on our website.
Have you seen what we saw?