Author: howard
Howard Precision Metals – The Ultimate Aluminum Supply Company
Howard Precision Metals opened its doors in March of 1928. Since then, providing premium metal products with exceptional customer service, fast lead times, and at a fair price have been the mission. Though initially opened as a red metals distributor, Howard Precision is now a 100% aluminum service center and home to more saws under one roof than any other distributor in the United States. Read more to find out how the aluminum professionals at HPM can assist you with your aluminum needs.
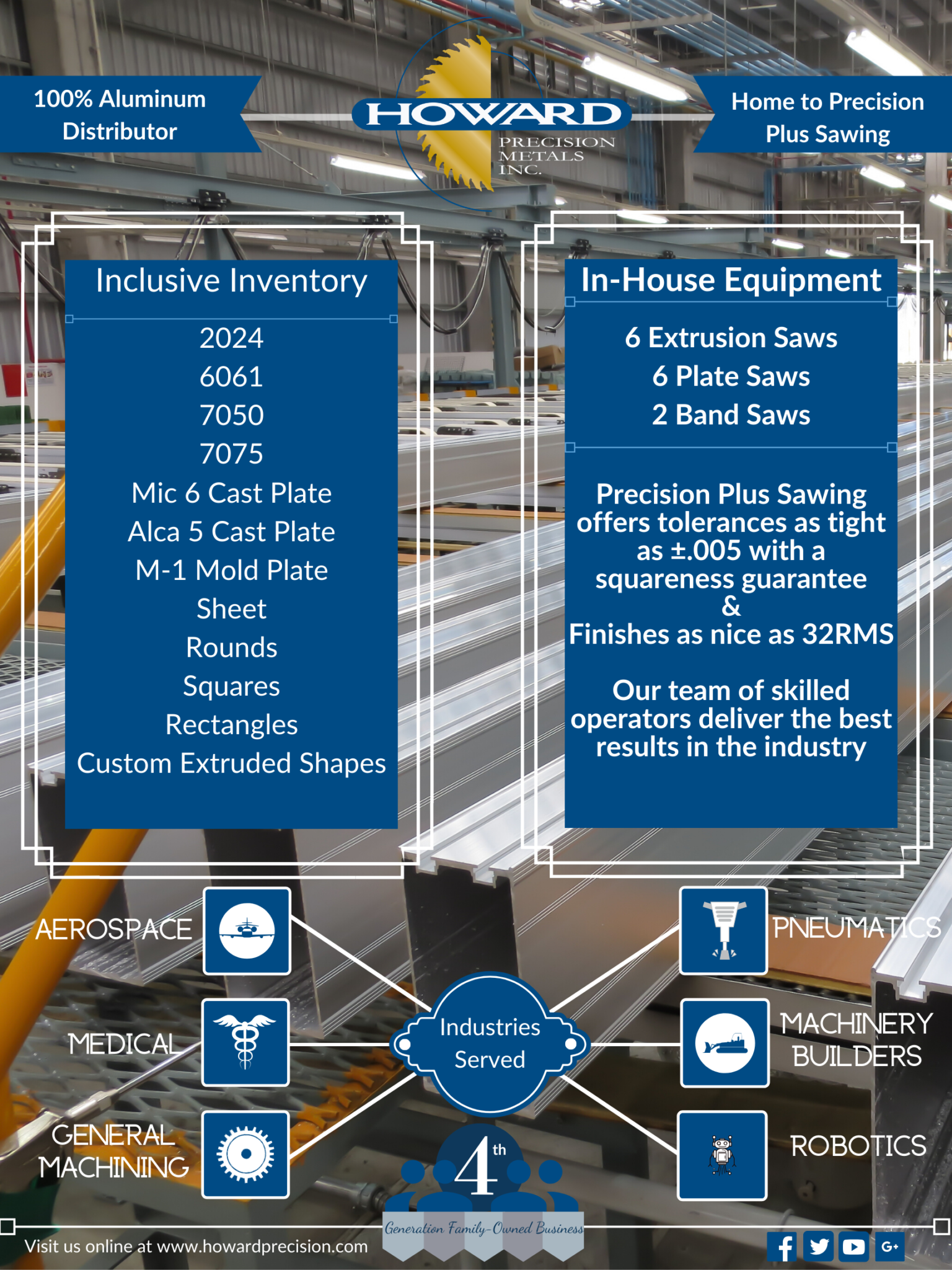
Premium Products and Knowledgeable Team
When you purchase any raw material, you want to be certain that you are getting a quality product. Aluminum purchasing is no different. That’s why it is crucial to purchase from distributors dedicated to quality and performance. At Howard Precision Metals, we pride ourselves on offering the best. That’s why we are committed to building and maintaining a reputation as the premier aluminum distributor and service center. Unlike our competition, we are transparent in our mill sources and country of origin for all our products. We have found that customers really appreciate knowing what they are receiving before it arrives. We have very stringent quality standards. Not only must mills meet our quality standards to be a source of ours, but they must continually perform to remain onboard. Every pound of our aluminum products is 100% traceable back to the parent plate or bar. This includes every single piece of metal available for sale on our Random Rack! Not only is our inventory top tier, but we have the best Team in the industry. Our aluminum experts are here to make sure that you get not only what you request, but what you actually need. From our Packaging Department to our Sales Team, you will not find another group of more dedicated and knowledgeable individuals. We know aluminum, because aluminum is all we do.
Home to Precision Plus Sawing
We figured it’s best to tell people what we’re all about. That’s why we put the word “Precision” in the name. That’s also why our Precision Plus sawing found its name. What is Precision Plus sawing? It’s a culmination of some very simple yet very important things. First, we start with custom built, high-speed, aluminum plate saws. When you have been doing this as long as we have, you learn a thing or two about what makes a performance sawing machine. That’s why we have our saws custom designed and built to our specifications. Our equipment is as rare as our quality. Next, we purchase only the very best aluminum products from the most reputable sources. Finally, you need our team. It’s not just about the sawing equipment or the aluminum. Precision results are only achieved by skill, knowledge, and dedication. That’s why we so effortlessly produce tolerances as tight as ±.005” and saw finishes as nice as 32 RMS. What’s even better? We guarantee squareness tolerances, too. Not only can we produce these results on wrought and cast tooling plate, but we also produce these results on aluminum extruded bar stock. Our 6 in-house precision extrusions saws stay busy cutting manifold blocks for the hydraulic industry as well as sawing heads and caps for the pneumatic industry. With more sawing capacity under one roof than any other service center in the Midwest, we have the skill and capacity to tackle any aluminum requirement.
Robust & Inclusive Inventory
Though our inventory is comprised of only aluminum, it is extremely inclusive. Wrought aluminum plates are available in thicknesses from .25” thick and up through 10.0” thick. We include alloys 2024, 6061, 7050, and 7075. Alpase’s M-1 mold plate is our primary choice for mold plates. M-1 is available in thicknesses of 1.5” and up through 10” thick in house. If you need larger plates, Alpase will cut to size and ship your aluminum mold plate order directly to you. If flat plate is what you need, we have you covered with our aluminum cast tool and jig plate. We stock both Mic 6 and Alca 5 cast plate products. Both CT&J options are available in .25” through 4.0” thick. As a bonus, our Mic 6 is also stocked in metric thicknesses. We always keep the following metric thicknesses on-hand: 6mm, 10mm, 15mm, 20mm, 25mm, and 30mm. Need thinner material? We have your back. Aluminum sheet is also available in alloy 6061. Finally, aluminum extrusions are plentiful. We stock a wide range of extruded aluminum squares, rounds, rectangles, and even all the NFPA standard sizes for our Hydraulic and Pneumatic customers. If you can’t find the bar size you need, don’t fret. We can have custom sizes and even complex custom shapes tooled and produced within a reasonably fast turnaround. Our mill partners provide the best custom aluminum extrusions available. For any aluminum requirement, large or small, we can handle them all.
Ryerson founded in 1842 acquires Howard Precision Metals founded in 1928 and the deep tradition continues. Although no longer privately held, Ryerson together with Howard Precision Metals remain focused on superior customer service and continuing to increase value as your preferred metals service center. With a focus on technological improvements to increase efficiency and drive excellent results, the future of Howard Precision Metals is shining brightly.
Contact Us Today
For any aluminum requirement, trust the expert team at Howard Precision Meals. Let our talented Sales Team help you with your next project. Give us a call at 800-444-0311 or request a quote today.
Howard Precision Metals – A Premier Provider of Aluminum Bar
An In-depth Look at 2024 Aluminum from Howard Precision
Howard Precision Metals – Metal Sawing Services
The Premier Aluminum Saw House
Our custom built, high-speed, proprietary designed aluminum plate saws are highly coveted in the marketplace. These high performance, precision machines are capable of sawing a range of aluminum sheet and aluminum plate in thicknesses of .063″ up through 10.00″. Our saws are operated by highly skilled technicians and meticulously maintained. This enables us to deliver what Team Howard refers to as “Precision Plus Sawing.” Not only that, our aluminum is sourced from only the best of the best aluminum mills. We ensure that only high quality materials are procured from our sources. With such attention to detail, we deliver saw tolerances as close as ±.005″ and offer squareness guarantees as tight as .005″, 12″ from any Howard Precision sawn corner. Our reputation for providing premier aluminum sawing services along with top-quality aluminum products to our customers is why we are still “A Cut Above The Rest” after more than 90 years in the metals industry.
Precision Aluminum Plate & Extrusion Saws
In addition to our aluminum plate saws, we also have six custom aluminum extrusion saws. These in-house saws help us to meet tight turnaround times, even on large production sawing orders. Like our aluminum plate saws, our extrusion saws are also capable of holding saw tolerances as tight as ±.005″. Our sawing equipment has the ability to saw extruded aluminum rectangles and square bars in thicknesses of .090″ through 8.00″ thick. In this size range, we achieve surface finishes as close as 32 RMS. The right equipment and premium products allow us to deliver premium sawn aluminum extrusions to our customers with ease.
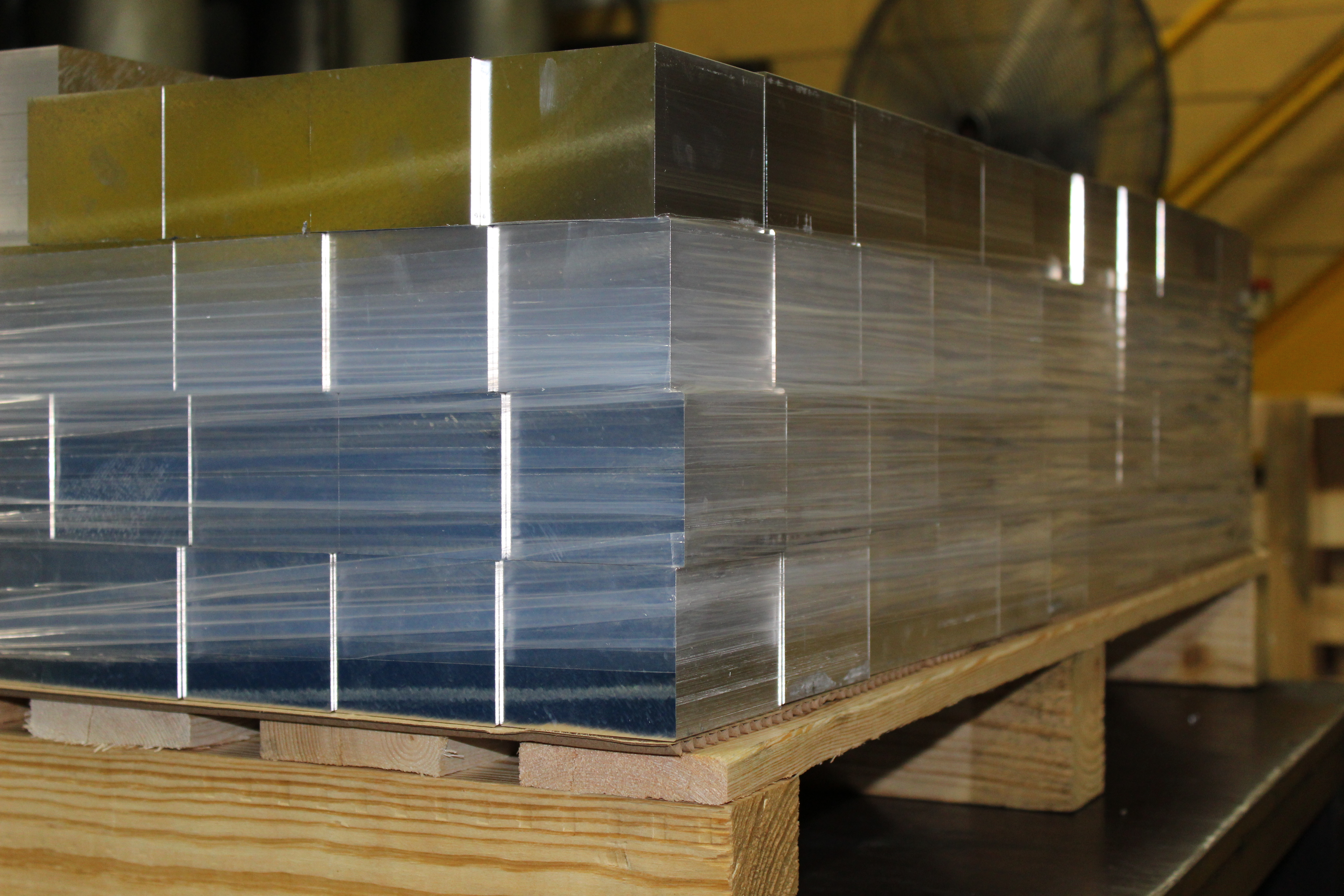
Aluminum Band Saws
For larger aluminum extrusions including large diameter solid round stock, we are also equipped with two aluminum band saws in house. These massive band saws increase our sawing capacity tremendously. How? These larger than life pieces of sawing equipment allow us to bundle cut large quantities of aluminum extrusions. This is extremely efficient on aluminum extrusion items where sawing tolerances are not critical. Capable of cutting material as large as 22″ diameter, these workhorses can achieve tolerances of ±.030 and surface finishes as close as 76 RMS.
Type of Aluminum Saw | Quantity in House | Thickness Capability | Width Capability | Sawing Tier | Tolerance Level | Squareness Level** | |
Precision Plus Aluminum Plate Saws | 6 | 10.00″ maximum | 144″ maximum | Precision* | ±.005″ | .005″ | |
Intermediate | ±.010″ | .010″ | |||||
Utility | ±.030″ | .030″ | |||||
Aluminum Extrusion Saws | 6 | 8.00″ maximum | 24″ maximum | Precision* | ±.005″ | .005″ | |
Intermediate | ±.010″ | .010″ | |||||
Utility | ±.030″ | .030″ | |||||
Aluminum Band Saws | 2 | 22″ maximum | 22″ maximum | Band Sawing | as close as ±.030 | N/A |
*Precision sawing capabilities vary with plate thickness. Thicknesses of 2.76″ through 5.99″ will be guaranteed a tolerance of ±.010, while aiming for ±.005; Thicknesses 6.0″ through 8.0″ will be guaranteed a tolerance of ±.030, while aiming for ±.010; Thicknesses over 8.0″ will be sawn to a plus side only tolerance to allow for machine stock. **Squareness on aluminum plate is measured within 12.0″ from any Howard Precision Metals sawn corner. Squareness on aluminum extrusions is relative to the straightness of the mills’ products, in combination of the length of the material.
Contact Us
For your next aluminum sawing requirement, trust the experts and custom equipment only available at Howard Precision Metals. With more saws under one roof than any other aluminum distributor in the Midwest, we have the capacity to deliver even the largest orders with ease. Contact us today at 800.444.0311 or request a quote today.
Have you seen what we saw?
Aluminum Plate or Sheets? What’s the Difference?
Aluminum offers a multitude of benefits, including being lightweight and having high corrosion resistance. It comes in the form of plates or sheets, both of which can continuously be recycled without any loss of properties, and can be used for a wide array of industrial applications.
Plates and Sheets
As aluminum moves between rolls under pressure, it becomes longer and thinner, thus resulting in Aluminum Plate or sheets. One of the main differences between Aluminum Plate and sheets is that sheet metal is under .249” thick, while plate metal is .250” and above.. Another difference between Aluminum Plate and sheets has to do with the distinct applications for which they are used.
Sheets
Sheet is the form of aluminum that is used the most often. You can find it in all of the major markets of the aluminum industry. For instance, aluminum sheet is useful for manufacturing packages and cans in the packaging industry. It is also valuable for manufacturing tractor trailers and automobile body panels in the transportation industry. Sheets are also useful for cookware and home appliances, as well as for construction/building products, such as carports, awnings, roofing, gutters, and siding.
Sheet aluminum can even be given blue, red, gold, or black colors, for instance, through color anodizing. It can also be etched to feature a matte finish, or be polished to feature a bright, sparkling appearance. Aluminum sheets may additionally be made to resemble wood through texturing.
Plates
Aluminum plate is the most often used for heavy-duty applications, particularly in the transportation product manufacturing, aerospace and military industries. Since certain aluminum alloys have the potential to become more durable at extremely cold temperatures, Aluminum Plate serve as the skin of spacecraft fuel tanks and jets, and can also be useful for storage tanks. Moreover, you can use Aluminum Plate in the manufacture of structural sections used in ships and railcars and for military vehicle armor.
Howard Precision offers aluminum plate along with many other forms of aluminum products that are designed to suit your specific needs. Our company focuses on providing quality so our customers can have access to top-tier aluminum products each time they need them.
Amazing Aluminum
The production of aluminum first starts with the mining of bauxite, a clay-like soil found all around the Equator. Alumina, or aluminum oxide, is extracted from the bauxite during the refining process, after which it is smelted to form liquid aluminum. It is then cast into extrusion ingots, sheet ingots or foundry alloys, depending on the intended end use.
Aluminum Plate
The production of aluminum plate starts with large sheet ingots, weighing up to 20 tons each. These ingots are first heated to soften them enough for rolling, before being fed into a breakdown mill. Here they are rolled back and forth until they become just a few inches thick.
These slabs are then either cold rolled, or heat-treated to strengthen the metal. The highest strength alloys are cooled, then stretched and straightened to help relieve any internal stresses that may have built up during the process thus far. They are either left to age naturally at room temperature, or placed in a furnace to develop strength and corrosion resistance, before finally being cut into plates. All these different processes are defined by the temper designation of the material.
Types of Aluminum Plate
6061 aluminum plate is part of the family of heat treat alloys which is harder and more machinable than the common alloys like 5052 & 3003. 6061 is comprised of magnesium and silicon as its alloying elements. Of all the heat-treated aluminums, 6061 aluminum plate has the highest resistance to corrosion, but it is not as strong as some of the other heat treated alloys.
It has good forming properties, welds easily and has excellent joining characteristics. It can easily be cut, stamped, tapped, deep drawled or drilled using standard methods.
6061 is used in a wide variety of applications, including in the production of canoes, sailboats, trucks, buses, transmission towers, furniture, marine and chemical equipment, mine skips and hardware.
6061 T651 is an excellent, versatile alloy, suitable for all purposes. It has good weldability and strength, as well as good resistance to corrosion and good machinability. It has an ultimate tensile strength of at least 42,000 psi, an ultimate shear strength of 27,000 psi, and a yield strength of at least 35,000 psi.
Step Up to the Plate
Aluminum is the most widely used metal in the world after steel. When alloyed with one or more of a variety of other metals, it becomes a lightweight, strong and durable metal suitable for a wide range of products across numerous industries.
Aluminum comes in a variety of shapes and sizes, including rod, tubing, sheet and plate.
Aluminum Plate
The only difference between aluminum plate and sheet is their thickness. Aluminum that ranges in thickness from 0.008 inches to less than 0.25 inches is considered sheet. Anything thicker than this is plate, and anything thinner is foil.
Aluminum plate (and sheet) can be recycled continuously without losing any of its properties, or weakening in any way. Recycled aluminum is indistinguishable from primary aluminum, but requires only 10% of the energy to produce.
Military grade aluminum armor plate is highly valued for its impressive performance standards. It can, for example, deflect a .50 caliber round that would pierce other metals.
How It’s Made
Preheated ingots of aluminum (typically about six feet wide, 20 feet long and more than two feet thick) are passed between rollers under pressure. The ingots become thinner and longer in the direction in which they are moving.
They may be heat-treated to increase their strength, but generally, aluminum plate is at its strongest when it is at its coldest, which is why it is often used for storage tanks. However, it does also perform exceptionally well under extremely high temperatures, and is commonly found around the engine of commercial and military aircraft, where temperatures of up to 250°F (121°C) are frequent.
2024 Aluminium Plate
2024 aluminum is one of the most popular alloys in production today. It has copper as its main alloying element, and offers several desirable properties, including:
- Good resistance to pressure
- High strength-to-weight ratio
- Good weldability, but only through friction welding
Like all alloys in the 2000 series, 2024 aluminum is vulnerable to atmospheric corrosion, especially if being used in an industrial or coastal environment. Cladding these alloys is a highly effective way of solvng this problem, making the surface resistant to corrosion, while adding extra cathodic protection.
Aluminum Extrusion Shows Off the Versatility and Usefulness of Aluminum
Perhaps one of the most underrated innovations of modern manufacturing is an aluminum extrusion. This process allows aluminum and specially-created aluminum alloys to be precisely formed into an almost limitless variety of shapes. These shapes can then be put to use in a number of different mechanical and decorative ways, furthering the many beneficial qualities of aluminum extrusion.
How Aluminum Extrusion Works
Any child who has ever put Play-Doh through the “Play-Doh Factory” has basically seen how an extrusion process works. You put a formable material in one end and pull or push it through a shaped die until it comes out the other end. An almost unlimited number of possible aluminum extrusion shapes can be created. The piece can then be precision cut to the length you want, giving you exactly the size you need. No matter where along the piece a cut is made, the cross section will be exactly the same. So a long run of extruded material could be used as one long piece, or numerous smaller pieces with identical cross sections.
Extrusion Alloys
Most often pure aluminum is not what you need for custom aluminum extrusions. Creating an alloy by combining aluminum and another element can increase the strength, formability, weldability or corrosion resistance of the finished product. Some of the other materials that aluminum is frequently combined with can include copper, zinc, manganese, magnesium, silicon, nickel, iron and chromium. For extrusion purposes, the alloy usually has an aluminum content of at least 93 percent.
Uses for Extruded Aluminum Pieces
The aluminum extrusion process can create virtually any shape you need in an aluminum form, which means its uses are widely varied. Perhaps the most common application we see an extrusion in are window and door frames or trailer and piers. Their combination of length and precise shape is difficult to create through other methods without creating seams that could leak or rupture along the length. For similar reasons, pipes and ductwork are often made through the extrusion process. Simpler heavier extruded shapes are often used to minimize machining operations that require tighter tolerances than an extrusion can offer. Using an extrusion in this application reduces both material and machining time.
Product designers, architects, and contractors can derive many benefits from working with extruded aluminum. Extruded aluminum products are a popular choice for businesses in many industries for a variety of reasons, including its versatility and ease-of-use. Some of the benefits afforded with aluminum extrusion include:
Reduce or Eliminate Machining
The fewer parts involved, the simpler the design, and the fewer steps involve result in products that are less expensive to manufacture. As an example, a part may be manufactured without the traditional use of machining through the use of a punch die instead, resulting in faster and lower cost production.
Reduce the Number of Required Parts
The design of complex shapes to reduce the number of parts required is possible through the use of extruded aluminum. A single aluminum shape produced through extrusion can substitute for multiple rolled shapes connected together through welding or another attachment method. This results in savings on connection costs and a potentially higher strength shape.
Adding Design Features
Extruded aluminum makes it possible to add design elements in construction applications. Examples include complex shapes such as grooves for windows. With the great flexibility afforded by aluminum extrusion, the design possibilities are almost endless.
Energy Efficiency
In the construction industry, aluminum, which includes aluminum products formed through the extrusion process, is one of the most energy efficient materials.
Surface Finish Options
There are various options available to enhance the surface of aluminum formed through extrusion. The material’s corrosion resistance can be enhanced through an applied pretreatment which helps ensure the material’s bond with the finish. The options for finishing include grinding, anodizing, blasting, painting, plating, buffing, polishing, and more. Two of the most frequently applied finishes to aluminum surfaces are painting and anodizing.
Recyclability and Reusability
For construction applications, particularly as property owners are opting for deconstruction and disassembly as opposed to building demolition, recyclability and reusability are becoming increasingly essential. Through disassembly or deconstruction, it is possible to capture the recyclable materials and preserve their scrap value. This lowers the cost of material landfill dumping and any associated negative environmental impact.
Conductive for Electricity and Heat
Applications involving heating/cooling and electronics can benefit from the heat and electricity conductive properties of aluminum.
Lightweight and Strong
Aluminum extrusions help users take advantage of the material’s strength and lightweight properties. With a strength-to-weight ratio of about one-third of the weight of steel and with a strength similar or greater than steel, aluminum is ideal for applications in which high load bearing is required but the support member(s) must not be too heavy.
Easy Workability
Many designs are possible with the use of dies. As a metal that is easy to work with, it is not too difficult to manipulate the material with tools. However, its strength is not affected by the fact that it is softer than steel, workable, and malleable.
If you need aluminum for any of your project applications, consider the versatility and usefulness of this material.
Aluminum Plate Makes the World a Better Place
Aluminum is a versatile metal that can be used for a wide variety of purposes. It can be combined into a number of different alloys that expand its usefulness even more. In plate form, aluminum is especially useful in the aircraft industry, but it’s also used for automobiles, storage, construction and other areas that strive to improve our daily life.
Aluminum Alloys
On its own, aluminum has a number of useful properties. It’s reflective, ductile, malleable, non-magnetic and completely recyclable. It is also strong and light in comparison to steel and resistant to corrosion. To build on those properties, aluminum is sometimes mixed into an alloy with other metals. Aluminum is generally combined with magnesium, silicon, manganese, tin, copper and zinc to form alloys. The advantages of these alloys can include lowering the melting point and increasing the strength, ductility, and resistance to temperature extremes.
Aluminum in the Aircraft Industry
The strong and lightweight nature of most aluminum alloys makes them perfect for aircraft use. Aluminum plate is often used to make the aircraft skin as well as other elements like fuel tanks, internal compartments and storage areas. Structural elements can be made from 6061 T6 aluminum plate. Aluminum is also used in making smaller parts like control panels and instruments, bolts, and fixtures. Generally, higher-strength alloys such as 7050, 7075, 7175 and 7475 are most popular in the aircraft industry.
Other Products that Use Aluminum Plates
For the same reasons the aircraft industry uses aluminum, aluminum plate suppliers also tend to sell a lot to the automotive industry. Everything from structural elements to engine crank cases may be made with aluminum, while fuel tanks may be made from 6061 aluminum plate. You might also find aluminum plate for sale to be used for equipment such as road signs, storage lockers, or manufacturing applications.
Using aluminum alloys instead of other materials to make these products allows them to be lighter, resist corrosion, and be strong enough to have an extensive longevity. Moreover, aluminum is recyclable, which is an immense benefit to using such a material, in an economy that is becoming increasingly more environmentally conscientious.